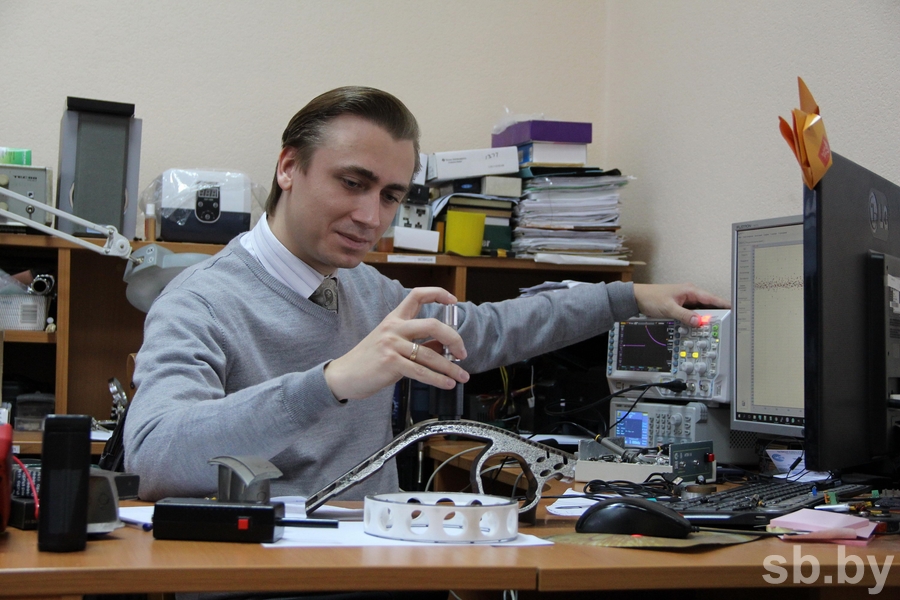
На рабочем столе Егора — фрагменты деталей жидкостного ракетного двигателя. Контроль покрытий различных узлов этого сложнейшего устройства — основная сфера его научных интересов. Ей посвящена кандидатская диссертация, которая сейчас в процессе написания, а за практические результаты в решении актуальных задач неразрушающего контроля покрытий ракетной техники он стал обладателем президентской стипендии. По словам Егора Гнутенко, ракетный двигатель — вершина технологий, изделие уникальное, как и применяемые в нем решения, материалы, покрытия:
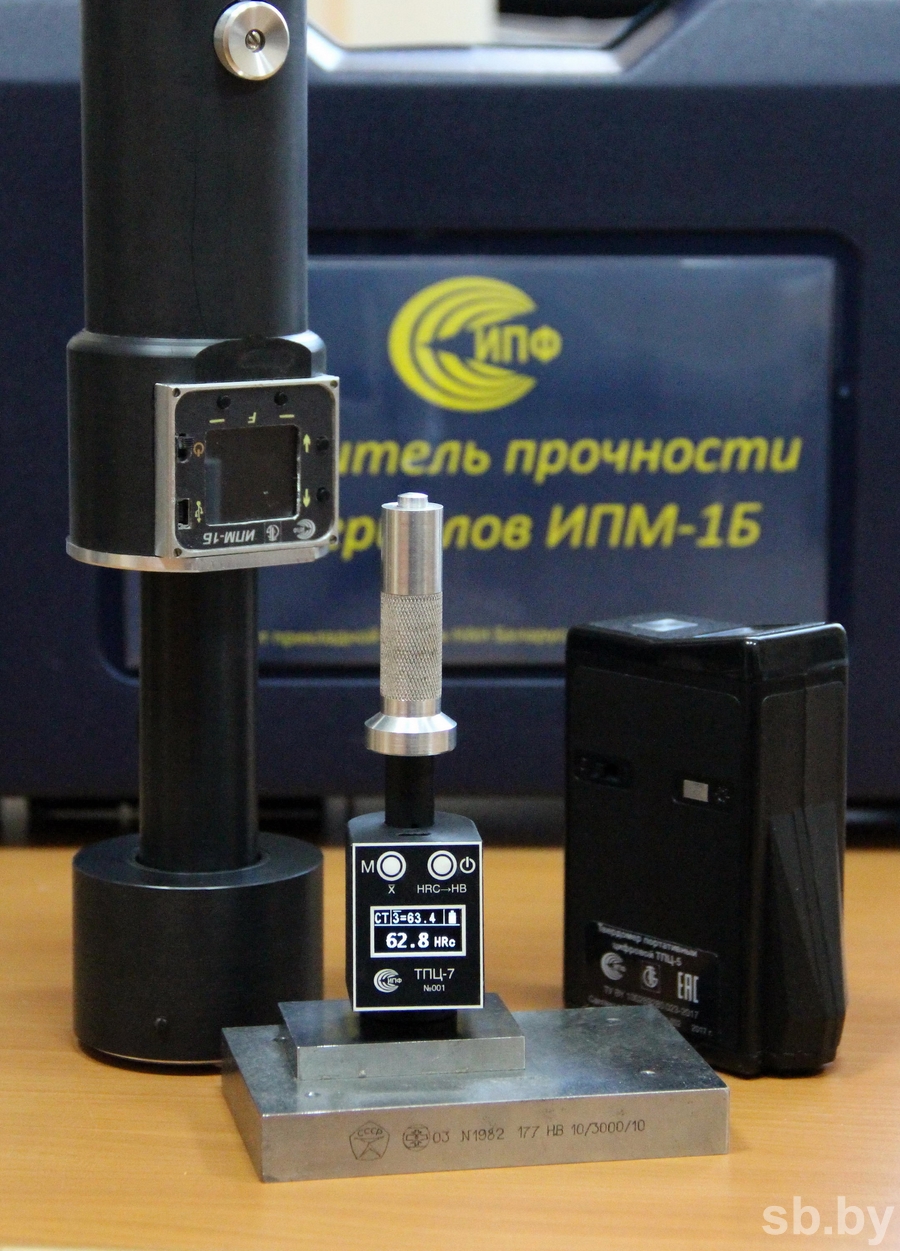
Метод, используемый для неразрушающего контроля в данном случае, называется пондеромоторным, или магнитоотрывным. Работает он, если описать совсем просто, так: магнит притягивается к никелевому покрытию, затем его отрывают и оценивают силу, при которой это произошло, — она и говорит о толщине. Но преломить этот, казалось бы, простой метод для аэрокосмической сферы крайне трудно, учитывая сложность изделий и сопутствующие мешающие факторы.
Егор Гнутенко берет в руки фрагмент сложной формы, колесо турбины с множеством лопаток: оказывается, это элемент одного из самых дорогих узлов ракетного двигателя — турбонасосного агрегата, стоимость которого доходит до сотен тысяч долларов. Он ответствен за прокачку компонентов топлива. Колесо делается из цельного куска металла по специальным технологиям. Чтобы привести его в движение, в него бьют реактивной струей. А чтобы не происходил его прогар, на колесо наносят специальное никелевое покрытие толщиной до 300 микрометров. Стоимость детали настолько высока, а потери, в том числе репутационные, при провальном запуске ракеты, столь огромны, что вопрос контроля качества выходит на первый план. Собственно, поэтому в первую очередь неразрушающий контроль находит себя в областях, где изделия дороги и в случае неудачи есть риск больших убытков: космос, авиация, энергетика. Исследователь говорит, что сейчас задача более сложная:
— Когда нанесено несколько покрытий, за один раз определить толщину каждого из них на готовом изделии. Двигатель — вещь многокомпонентная. Что–то делается на одном заводе, что–то — на другом. И когда это все прибывает в финальную точку сборки, стоит задача входного контроля. Сейчас мы плотно работаем с Санкт–Петербургским национальным исследовательским университетом информационных технологий, механики и оптики, совместно создаем установки для автоматизированного контроля.
Установки для автоматического контроля помещаются внутрь двигателя. Они сами перемещают датчики по кривизне его камеры сгорания и контролируют множество точек. Это поможет также прогнозировать, каков будет остаточный ресурс, как покрытие поведет себя в дальнейшем. А этот вопрос часто задают ученым.
Свой метод
Еще один способ узнать о материале все — твердость, прочность, вязкость, упругость, стойкость к деформациям и прочее — в Институте прикладной физики называют собственным эксклюзивом. Речь о таком методе неразрушающего контроля, как динамическое индентирование. Суть его в следующем: на исследуемую область объекта падает боек, и по характеру его взаимодействия с поверхностью определяются ее свойства. Взять трубопровод. Он находится под давлением, но вдруг возникает трещина. Вопрос: произойдет авария или нет? С помощью метода динамического индентирования можно оценить способность металла сопротивляться развитию трещин, понять, достаточна она или нужны экстренные меры. Этот же способ помогает контролировать прочность бетона, в первую очередь на таких ответственных сооружениях, как мосты и опорные конструкции. Работает он и на космос. В космических аппаратах, которые эксплуатируются в сложнейших условиях, при температуре —200 градусов Цельсия, в качестве материалов для уплотнителей используется не резина, а особый углеродный материал: пирографит. Если он разрушится — потеряется герметичность, а это чревато аварией. Поэтому материал и проходит жесткий контроль.

Первый в СССР портативный динамический твердомер был придуман и сделан именно в Институте прикладной физики еще в 1970–е годы — в одно и то же время, когда схожие приборы стали появляться за рубежом. С тех пор нашими физиками создана и постоянно пополняется целая линейка программно–аппаратных комплексов, применимых к металлу, полимерам, композитным и углеродным материалам, бетону и другим материалам. Такие приборы отличаются высокой точностью, а по цене на 30 — 40% дешевле российских аналогов. Потребность в них постоянно растет. Однако в лаборатории контактно–динамических методов контроля не скрывают, что главной целью считают не масс–маркет, а производство эксклюзивных приборов, для решения нетипичных задач, с которыми невозможно справиться имеющимися на рынке средствами. Егор Гнутенко приводит свежий пример:
— Для ОАО «Белшины», нашего гиганта, мы сейчас разрабатываем систему мониторинга температуры в шине — при испытаниях на стенде. Предприятие изготавливает сверхкрупногабаритные шины для карьерной техники, в том числе для БелАЗов. И когда отрабатывается технология их производства или меняется состав резины, важно знать, как шина ведет себя в процессе испытаний, каждую минуту отслеживать температуру в толщине резины. Готовых решений для такой задачи просто не существует.

Идти от идеи к реализации помогают сильная научная школа, многолетние исследования, хорошая приборная база и штучные кадры.
КСТАТИ
Институт прикладной физики совместно с Институтом физиологии Национальной академии наук начали оригинальный проект, в результате которого на свет должен появиться умный тренажер равновесия, доступный широкому кругу потребителей. Его основа — диск, «нашпигованный» датчиками, на котором нужно будет удерживать равновесие и выполнять упражнения. Задания даст смартфон, он же с помощью специальной программы оценит их выполнение. В упражнениях на равновесие задействованы многие системы организма, что улучшает координацию, память, внимание. Плюс такая платформа поможет тренерам перед соревнованиями определить, какой из спортсменов находится в наилучшей физической форме.
vasilishina@sb.by