
Модернизация Оршанского льнокомбината, где трудится более 4 тысяч человек, началась в 2007-м. Объем вложений, государственных и собственных, оценивается более чем в 100 миллионов евро. Самое значительное обновление прошло в течение последней пятилетки, когда были переоснащены фабрики № 2 и № 3. Появилось новое импортное приготовительное и ткацкое оборудование. Условия труда стали гораздо более комфортными. К примеру, ткач 5-го разряда Алла Сулимова, работающая на предприятии более 20 лет, признается, что по-новому влюбилась в свою профессию:
— Раньше тканые рисунки на жаккардовых станках мы создавали при помощи своеобразных картонных трафаретов. Не передать, сколько трудов и времени уходило, чтобы подготовить такой трафарет для создания 2,5-метровой скатерти! Для хранения трафареты складывали гармошкой. Они рвались. А вот новые жаккардовые машины компьютеризированы. Достаточно загрузить рисунок с флешки в диалоговую панель — и умный станок готов к работе! Производительность выше, нет брака, цветовая палитра шире. Любому заказчику мы сразу продемонстрируем, как будет выглядеть его изделие. Даже его портрет по фотографии выткать можем!
В ткацком цехе фабрики № 2 в этом году появились 36 таких станков. Растут и зарплаты ткачих. У Аллы Сулимовой, например, она превысила 800 рублей. Это с учетом сложностей, связанных с переоборудованием цеха. Но без модернизации сегодня не обойтись. Именно она позволила предприятию из средних номеров льноволокна получать продукцию более высокого качества, снизить себестоимость, расширить ассортимент. Сегодня комбинат выпускает около 2 тысяч артикулов тканей. Иначе конкурентную борьбу с китайскими и индийскими производителями не выиграть.
Качество конечного продукта, уверяют специалисты, процентов на 70 зависит от того, как лен посеяли, вырастили, собрали и обработали. Чтобы проследить за процессом с самого начала, я отправился на Бешенковичский льнозавод. Сегодня это филиал шумилинского сельхозпредприятия ОАО «Приозерный мир». Интересно, что маленький заводик, образованный в деревне Двуречье в 1932-м, по проценту выхода длинного льноволокна (5,19) на Витебщине уступает лишь Дубровенскому льнозаводу, где в 2006-м была установлена современная бельгийская технологическая линия. В Двуречье же льнотресту обрабатывают на агрегатах, выпущенных в 70-е годы прошлого века. Один из самых квалифицированных работников предприятия, оператор поточной линии по выработке длинного волокна Елена Коваленок на заводе трудится с 1984-го:
— Всем премудростям профессии я в цехе выучилась. От нас зависит, насколько волокно будет красивым и качественным. И какие деньги предприятие получит. Мой заработок — более 400 рублей в месяц. Для сельчанина, у которого подсобное хозяйство имеется, неплохо.

По словам директора Бешенковичского льнозавода Надежды Бокиш, льна по сравнению с крупными коллегами они сеют немного:
— В этом году — 400 гектаров. С Дубровно, у которого 2 тысячи, не сравнить. Однако нагрузка на наших пятерых трактористов падает колоссальная. Бывают моменты, когда в поле даже кочегаров отправляем, у которых водительские права имеются. Людей не хватает. Часть работников привозим из райцентра. Ничего не поделаешь. Молодежь из деревни, где из всей социалки лишь магазин остался, давно разъехалась.
В поисках общего знаменателя
Третья часть посевных площадей льна сегодня — на Витебщине. Там же расположена треть льнозаводов. Анализ, проведенный государственным объединением «Витобллен», показал, что в области сев в среднем занимает 20 дней, теребление — 40, а прессование — 67. Хотя по регламенту на каждую технологическую операцию отводится по 10. Но как уложиться в сроки, если не хватает льнотеребилок, половина тракторного парка изношена на 80 процентов? К тому же из 12 технологических линий по выработке длинного волокна в области 8 имеют стопроцентный износ. Вот и получается, что наши льнозаводы поставляют в Оршу длинное волокно средним номером 10,5. Но тонкую ткань, к примеру для сорочек, по словам исполняющей обязанности генерального директора Оршанского льнокомбината Ольги Неводничей, делают из волокна 12 — 13-го номера:
— В нынешнем году нам требовалось 7400 тонн длинного волокна. Это — госзаказ. А волокна с номером 12 и выше наши льнозаводы за 11 месяцев поставили лишь 332 тонны. А нам ведь надо загружать новое высокопроизводительное оборудование, расширять ассортимент. Вот и приходится волокно высоких номеров закупать по импорту.
Может ли страна в принципе обеспечить себя длинным волокном?
— Теоретически — да, — считает Ольга Неводничая. — В 2004—2005 годах мы работали на белорусском волокне. Но чтобы льнозаводы получили качественное сырье, необходимо строго соблюдать сельскохозяйственные регламенты.
В Минсельхозпроде ответственности с себя за невыполнение госзаказа не снимают. Однако, по мнению заместителя министра Владимира Гракуна, обвинять сельчан в том, что они сработали плохо, неправильно:
— Порой, как в этом году, погода вносит коррективы. А бывает, что у льнозаводов, которые являются льновозделывающими организациями, просто не хватает финансов, чтобы вовремя купить удобрения, средства защиты растений, топливо. Здесь бы льнокомбинату их поддержать. Подсказать, в конце концов, какой сорт льна лучше вырастить. Но от оршанцев заводчане, как правило, лишь слышат: «Вы привезли плохое сырье, мы его не примем!» Поэтому мы выступаем за создание общей интеграционной структуры, которая бы контролировала весь процесс производства и избавила бы нас от обоюдных претензий.
Возможна ли такая структура, когда Оршанский льнокомбинат входит в концерн «Беллегпром», а льнозаводы подчиняются Минсельхозпроду? По словам Владимира Гракуна, общение на эту тему с коллегами ведется давно, вносятся различные предложения:
— Жаль, но ни с одним из них «Беллегпром» и льнокомбинат пока не соглашаются. Хотя у нас перед глазами есть пример сахарных заводов, которые создали себе сырьевые зоны и работают успешно. Этот опыт можно было бы взять за основу. А как назвать общую структуру — холдингом или еще как-то, не столь важно.
***
Пока же специалисты видят один выход — выполнять госзаказ. И — зарабатывать, вкладывая полученные деньги в развитие. Как это делают льнозаводы в Горках, Дубровно, Крупках, Уваровичах. Государство поможет. Комплексный план мероприятий по повышению эффективности льняного подкомплекса на 2018 — 2020 годы уже разработан. Но если на всех этапах технологической цепочки не будет грамотной организации труда и заинтересованности производителей, самые лучшие планы останутся простой бумагой.КОМПЕТЕНТНО
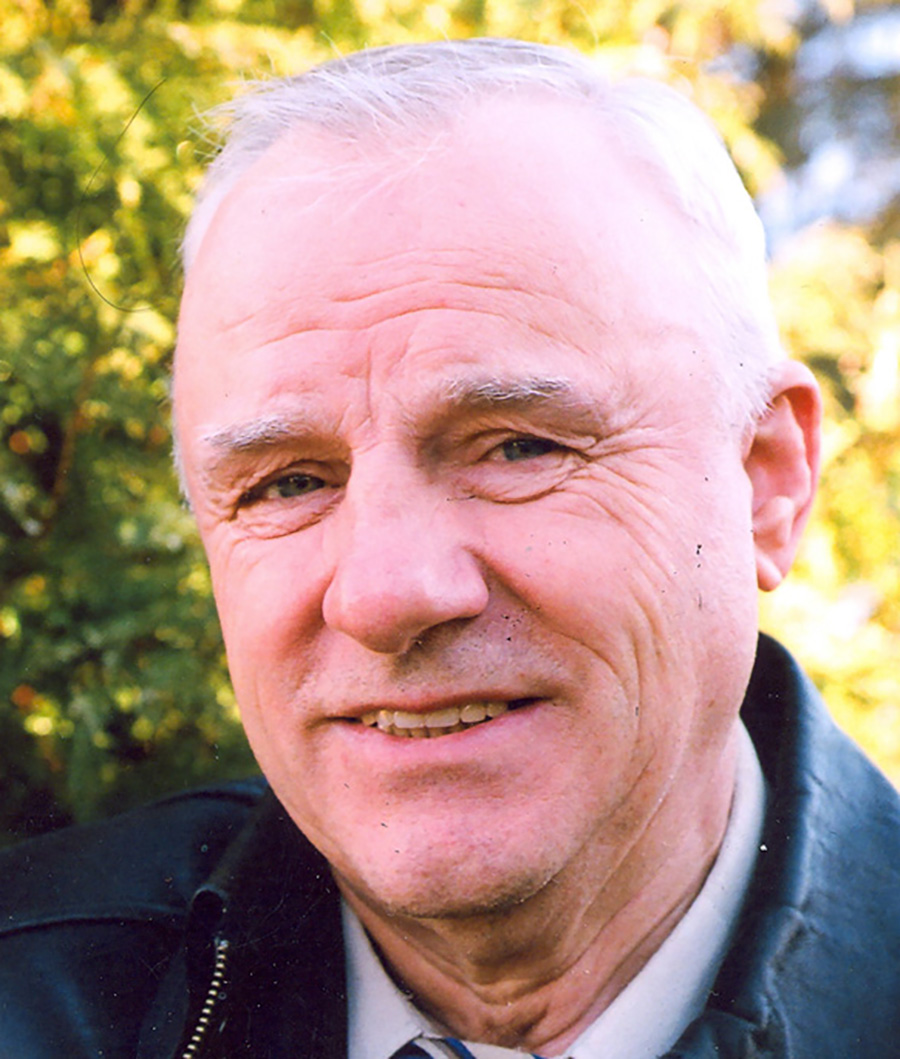
— Сейчас волокна с гектара мы получаем в 2,5 раза больше, чем 20 лет назад. Семян — в 2 раза больше. Выведенный нами сорт «гранд» успешно конкурирует с зарубежными и нашими аналогами. Да, по качеству волокна есть проблемы. Но имеющиеся наработки при дальнейших исследованиях и грамотном подходе помогут их решить.
svg-vt@mail.ru
Фота аўтара