Зерноуборочные комбайны последнего поколения и грубый цеп наших далеких предков, несмотря на свою кардинальную несхожесть, используют один и тот же принцип обмолота: выбивание зерна из созревшего колоса. Технология успешно просуществовала тысячи лет, но сегодня почти себя исчерпала. По крайней мере, такое мнение муссируется в научных кругах.
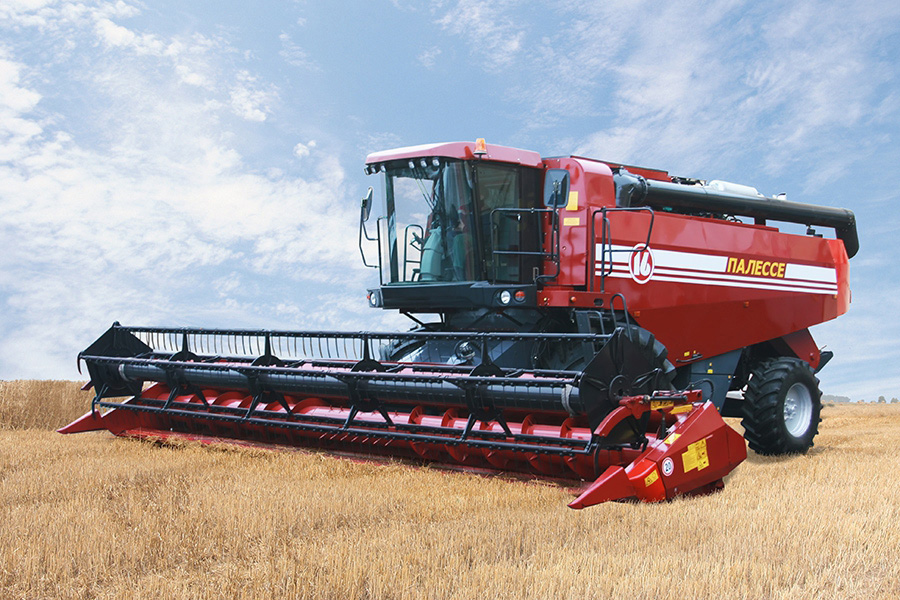
КЗС-1624-1 иногда называют комбайном будущего, но он уже работает на полях
Конечно, комбайн будущего появится не сегодня и не завтра. Возможно, через 5, 10 или даже 20 лет. Какой будет использован в них принцип работы — можно только догадываться. Но над новыми решениями уже всерьез задумались ведущие профильные мировые компании. Не исключено, что первые машины следующего поколения появятся на родных полях. Ведь белорусская школа сельскохозяйственного комбайностроения считается в мире одной из лучших.
Сельмашевская школа
Последние несколько десятилетий самоходная сельскохозяйственная техника наращивала энергонасыщенность. Если в начале века 150—200 лошадиных сил считались пределом, то сегодня в линейке ОАО «Гомсельмаш» уже есть модели комбайнов с силовой установкой свыше 600 «лошадок». Это почти предел.
Наращивание мощности, наряду с увеличением размеров рабочих органов, увеличивает производительность техники, но провоцирует другую проблему: машина становится слишком тяжелой для почвы. До поры до времени эту проблему удавалось решить разнообразными конструктивными инновациями: использовать более легкие материалы, ставить машины на новые широкопрофильные колеса или полугусеницы, которые снижают давление на почву… Но эти возможности уже почти исчерпаны.
Чуть ли не единственный способ повысить производительность — лезть внутрь машины. И пристально рассматривать не только все узлы и агрегаты, но и саму принципиальную схему комбайна. Наши конструкторы над этой темой активно работают. Перспективные планы расписаны на 5—6 лет вперед.
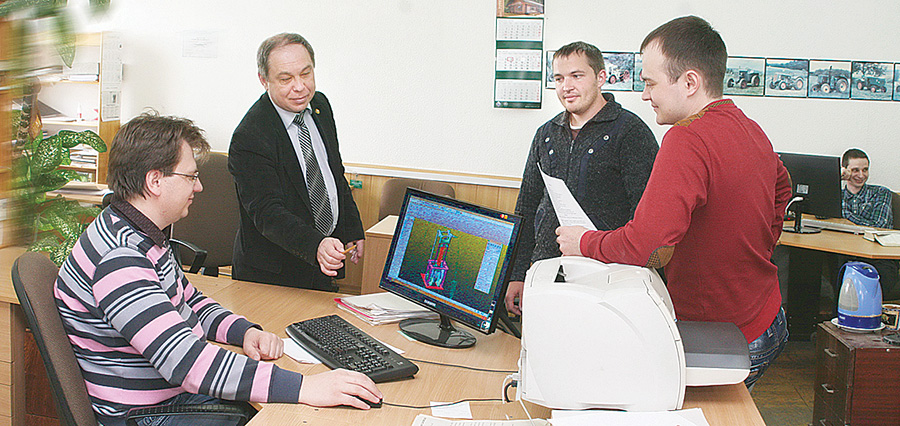
У сельмашевцев своя уникальная конструкторская школа
Конструкторы научно-технического центра комбайностроения (НТЦК) ОАО «Гомсельмаш» нащупывают принципиально новые решения. И оказаться первыми в этой мирной гонке сельхозвооружения шанс есть. Сельмашевская конструкторская школа за свою более чем 70-летнюю историю накопила огромный массив уникальных компетенций, которые позволяют ей конкурировать с аналогичными мировыми структурами. Кроме дипломов, наград и патентов, квалификацию наших отраслевых ученых подтверждает практика: все модели зерноуборочных комбайнов, разработанные НТЦК, пошли в серийное производство. Ни одна конструкция не оказалась тупиковой, не умерла на стадии опытного образца!
Все узлы в одних руках
Подходы отечественной конструкторской школы кардинально отличаются от западной. В иностранных корпорациях новые образцы техники собирают из уже готовых узлов и агрегатов, разработанных и изготовленных на специализированных предприятиях-смежниках. На «Гомсельмаше» происходит минимум заимствований извне: все детали разрабатываются в НТЦК и почти все производятся на главной производственной площадке. Импортные компоненты используются, только если их не удается произвести самим или отсутствуют белорусские аналоги.
И вот почему. Качество комплектующих нередко оставляет желать лучшего, а их дополнительный контроль требует немалых издержек. Начальник общетехнического комплекса НТЦК Виктор Сусов вспоминает: у потребителей первых белорусских самоходных кормоуборочных комбайнов КСК-100 было много нареканий на их надежность. При освоении этого комбайна было около ста заводов-кооператоров. И зачастую ломались именно «чужие» детали.
Когда их производство освоили на собственных мощностях, количество поломок резко снизилось. И сегодня наработка на отказ — до первой поломки — у наших зерноуборочных комбайнов «Палессе» составляет не менее 100 часов. Это значит, что при соблюдении правил эксплуатации техника может работать без ремонта практически весь уборочный сезон. Кстати, срок устранения отказов дилерами ОАО «Гомсельмаш» составляет не более суток.

Опытные образцы обретают серию на конвейере
Говорят, специализация снижает цену готового изделия. Но сотрудники НТЦК считают этот тезис далеко не однозначным. Хотя бы при сравнении базовых прайсов. Самая производительная сегодня белорусская модель КЗС-1624-1, которой под силу справляться с полями урожайностью 120 центнеров с гектара, стоит чуть более 300 тысяч рублей. А немецкий аналог — более миллиона рублей.
Технические же характеристики отличаются незначительно: по каким-то параметрам «белорус» проигрывает «немцу», по некоторым — опережает. Разница цены в три раза слишком серьезная, чтобы ее объяснить исключительно отличием стоимости рабочей силы в Беларуси и ФРГ и не совсем необходимыми опциями.
Универсальная структура «Гомсельмаша» и внедренная на предприятии электронная система управления ресурсами (SAPERP) позволяют оптимизировать расходы на производство техники и обеспечивают контроль затрат на всех этапах: от проектирования до сборочного конвейера и склада готовой продукции.
Чертежи новых деталей и агрегатов от конструкторов поступают к технологам, которые анализируют соответствие требований чертежа возможностям имеющегося оборудования и разрабатывают технологию изготовления изделий, на основании которой с учетом данных коммерческих подразделений по закупке материалов и комплектующих экономические службы определяют себестоимость изделия.
Получается гибкая система, при которой конструкторы ориентируются на имеющиеся мощности и производственные возможности, но в то же время, по заверениям Виктора Сусова, для повышения надежности машин достаточно часто в документацию закладываются решения, требующие модернизации производства и техперевооружения, что повышает конкурентоспособность гомсельмашевской техники.
Имея высококвалифицированное конструкторское подразделение НТЦК, «Гомсельмаш» не использует лицензионное производство узлов и агрегатов. Приобретение технической и технологической документации иностранных фирм стоит откровенно слишком дорого. К тому же чужие разработки могут таить ряд нюансов.
Джакузи в кабине
Иногда нашу технику критикуют: мол, проигрывает она импортной по уровню комфорта и функционалу. Определенная доля правды в этом утверждении есть. Но проблема не в мастерстве наших конструкторов или производственников. И первые, и вторые ориентируются не на какие-то призрачные рекорды, а на потребности и возможности потребителей.
Сегодня тот же «Гомсельмаш» способен насытить технику любыми типами датчиков, расширить функционал, оснастить рабочее место механизатора любыми гаджетами. Как иногда шутят в НТЦК, даже джакузи в кабину установить не является большой проблемой. Было бы у заказчика желание платить за эти чудеса техники. И потом тратить деньги на их ремонт и эксплуатацию. Ведь чем сложнее конструкция, тем выше риски выхода ее из строя. И ремонт дороже.
Виктор Сусов замечает: задача конструкторов — удовлетворить запросы любого потребителя. Если необходимая модификация отсутствует, а на нее поступил заказ — его необходимо выполнить. А ведь запросы у аграриев бывают очень разными. Особенно если учитывать, что наши зерно- и кормоуборочные комбайны поставляются более чем в 30 стран. И далеко не всем фермерам нужны большие и сложные машины.
Наоборот, в государствах Северной Африки, Ближнего Востока, Индии, многих провинциях Китая интересуются относительно простыми в эксплуатации и небольшими моделями. Кстати, многие западные предприятия их не выпускают, так как сориентированы на другие, более насыщенные финансами рынки.
С гордостью Виктор Сусов показывает модельный ряд «Гомсельмаша». По кормоуборочной технике закрыта вся линейка, по зерновой — практически все возможные позиции. Есть относительно простые, надежные, средней производительности зерноуборочные комбайны КЗС-575 и КЗС-812. Есть наиболее востребованные сегодня КЗС-1218 и КЗС-1218А-1. Есть энергонасыщенный КЗС-1624-1 — пропускной способностью свыше 16 килограммов хлебной массы в секунду.
Спросом у зарубежных фермеров пользуется машина с пропускной способностью 5 килограммов в секунду. НТЦК может создать и «кроху» в 3 килограмма в секунду. Есть в линейке модели на колесном и гусеничном ходу, с копнителем, с газовой силовой установкой… В прошлом году конструкторы создали еще 5 новых машин. Некоторые уже приняты госкомиссией.
Поедем в Европу!
Некогда кормоуборочная техника «Гомсельмаша» расходилась практически по всем странам социалистического блока. А в принципе, старые и надежные модели гомельчан помнят в Болгарии, Чехии, Венгрии — нынче уже странах ЕС. Зерноуборочные комбайны предприятие стало выпускать уже после развала Союза. В России и Казахстане доверие к нашей технике сохранилось.
А вот Европу сегодня необходимо покорять заново. Вроде бы при таком чудесном соотношении цена-качество белорусская техника должна пользоваться огромным спросом. Но рынок сельскохозяйственных машин очень консервативный. Большинство фермеров предпочитают покупать один и тот же бренд, если к нему нет тотальных нареканий.
Но лед в направлении ЕС тронулся. В Чехии уже работает дилер «Гомсельмаша», ряд моделей прошли сертификацию с правом нанесения СЕ-маркировки, уже работает около двух десятков машин. В первую очередь «Гомсельмаш» ориентируется на сельхозпроизводителей, которые не готовы переплачивать за громкое имя немецких и американских концернов. И собственная автономность (по крайней мере, пока) позволяет гомельскому предприятию достойно конкурировать с иностранными компаниями.
ПРЯМАЯ РЕЧЬ

— Сегодня НТЦК обладает всем необходимым для полного цикла конструирования и подготовки производства техники. Центр оснащен современными программно-аппаратными комплексами, которые позволяют проводить не только комплекс конструкторских работ, но и виртуальные испытания: можно «лечить» разные «болезни» еще на стадии проектирования. Есть своя хорошая производственная база для выпуска опытных образцов узлов, агрегатов и машин — экспериментальное производство. Стендовое и лабораторное оборудование, а также собственный полигон позволяют проводить все виды испытаний. Традиционно наш центр ориентировался на конструирование всех деталей, узлов и агрегатов. И отказываться от такой модели работы не собираемся. Например, для «Гомсельмаша» НТЦК разработал более сотни наименований редукторов. Зачем разработку и производство их отдавать на аутсорсинг, когда можем это изделие сделать сами?! Ведь это не только получение дополнительной добавленной стоимости, но и обеспечение занятости, повышение квалификации и компетенции специалистов. Это сегодня — один из важнейших факторов конкурентоспособности.
Скажем, гомсельмашевская конструкторская школа сельскохозяйственного комбайностроения накапливала опыт более семи десятков лет. Этот опыт удалось сохранить, обеспечить преемственность. Хотя сегодня приходится сталкиваться с проблемой утечки мозгов. Наших специалистов пытаются переманивать к себе на работу зарубежные компании. В первую очередь российские. И с ними тяжело конкурировать по уровню заработной платы, которая может отличаться в несколько раз. А ведь чтобы из выпускника вуза подготовить более-менее квалифицированного конструктора, необходимо 5—7 лет. И очень обидно, когда плодами этих усилий пользуются наши конкуренты.
Очень правильно, что руководство страны обратило внимание на развитие науки. Однако необходимо на государственном уровне поддерживать не только ученых фундаментальной науки, но и отраслевой. Ведь чтобы решить любую техническую проблему, нужно ее исследовать, изучить, найти оптимальный вариант из возможных, проверить его на практике. Фактически это тоже научная деятельность, хотя она далеко не всегда находит отражение в диссертациях и публикациях, но найденные решения воплощаются на практике в конкретных изделиях. И именно отраслевая наука является одним из важнейших стержней конкурентоспособности нашего машиностроения.
volchkovvv@mail.ru